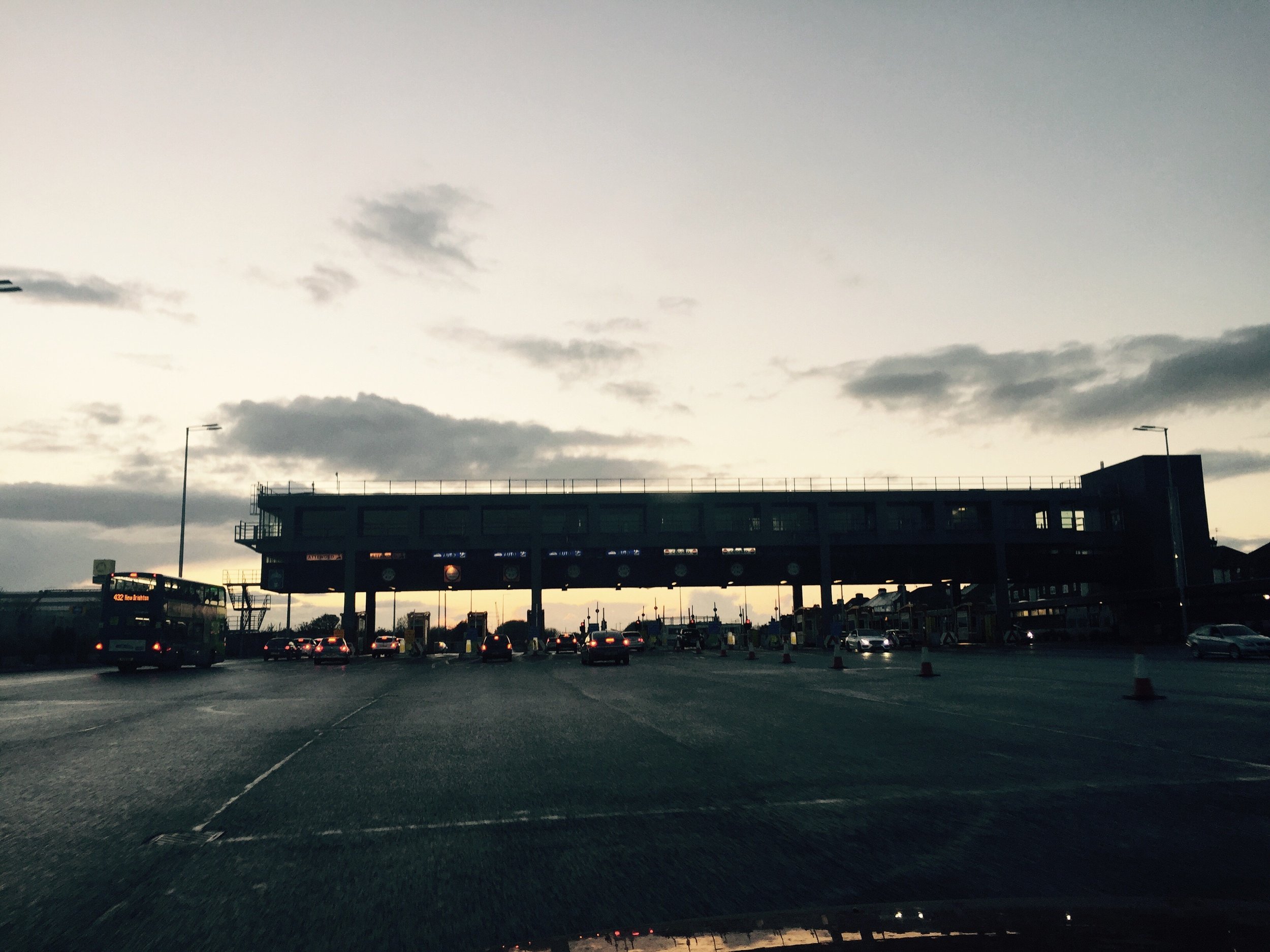
Upgrading the Mersey Tunnels’ Emergency Fuel Storage
Merseytravel owns and operates the two road tunnels beneath the River Mersey which provide the vital arterial connections between Wirral and North Wales, and the city of Liverpool and its docks.
-
Queensway tunnel was opened by King George V, in 1935 and this runs between Liverpool and Birkenhead. Queen Elizabeth II, his granddaughter, opened the second tunnel in 1971. Appropriately named Kingsway, this is located within two miles to the west, linking Liverpool and Wallasey.
-
Both tunnels have a number of ventilation shafts which are fitted with huge electric fans to extract fumes and maintain a continual supply of fresh air within the tunnels. The equipment has been updated progressively to improve efficiency and optimise energy. Variable speed motors allow the air flow to be managed to match the weather conditions, traffic density and to reduce consumption during off peak times.
The four ventilating buildings on the bank of River Mersey have back-up diesel electric generators which take over automatically in the event of a mains power cut. As well as maintaining ventilation the generators will provide back-up power for other essential services, such as the drainage pumps, lighting and communication. All of which are necessary for the safe operation of the tunnel.
“To ensure their availability, these back up facilities are run for three hours, every six weeks,” explains Adeola Kehinde, senior officer, Facilities and Works Department.
“We run under full load operational conditions for three hour periods to shake out any potential faults. Whilst these procedures have served their purpose over the years, the generator fuel storage facilities required upgrading. The design was out of date and the replenishment procedures were no longer compatible with best practice and the current regulations for the protection of the environment.”
“Another area that needed to be upgraded was the fleet fuelling point located at the operations support centre at Wallasey.
Merseytravel operates some fifty operation and utility vehicles and these facilities allow drivers to draw fuel whenever necessary, seven days a week.
“Having carried out an in-depth review of the sustainability and resilience of these facilities we put together a detailed recommendation to replace all the tanks filling point cabinets, install three new tanks, upgrade controls and centralised contents monitoring.”
The outcome of a thorough tendering process was a successful bid by Oil Tank Supplies who were awarded the contract in January 2011. The work was completed within 12 weeks against a tight schedule.
Adeola Kehinde credits this success to the work put in to the approval process and planning, saying: “The way the project was managed, tied in with what had been agreed and everybody was surprised and delighted with how it went in so smoothly.”
-
A new 20K litres bunded tank (double skin for total integrity) and associated replenishment controls were installed in six locations, covering each of the emergency power generators. The upgrade, in some cases replacing non conforming belly tanks, not only increased storage capacity, but it also simplified the replenishment process by removing the need for a top-up bowser. Each tank has been fitted with high and low alarms and electronic contents gauging to allow central monitoring.
The operations centre vehicle fleet fuelling forecourt was upgraded. This included relocation of the dispenser pump and the installation of a surface drainage interceptor to prevent oil spills and contaminated water from entering the storm drains. The pump was modified to allow remote monitoring of all the dispensing transactions, this together with new tank contents instrumentation enables the operations staff to reconcile fleet usage and stock levels.
-
The aim of the upgrade was to bring the overall fuel storage system into line with compliance to the current legislation for the storage of fuel oil. From an operational point of view the equipment provides instant information about the status of the tank contents.
As well as providing stores administration timely and accurate information for re-ordering, this also enables the control room staff to see immediate status of all the tanks and if necessary, to make better informed decisions to share loads and maintain services in the event of an emergency.
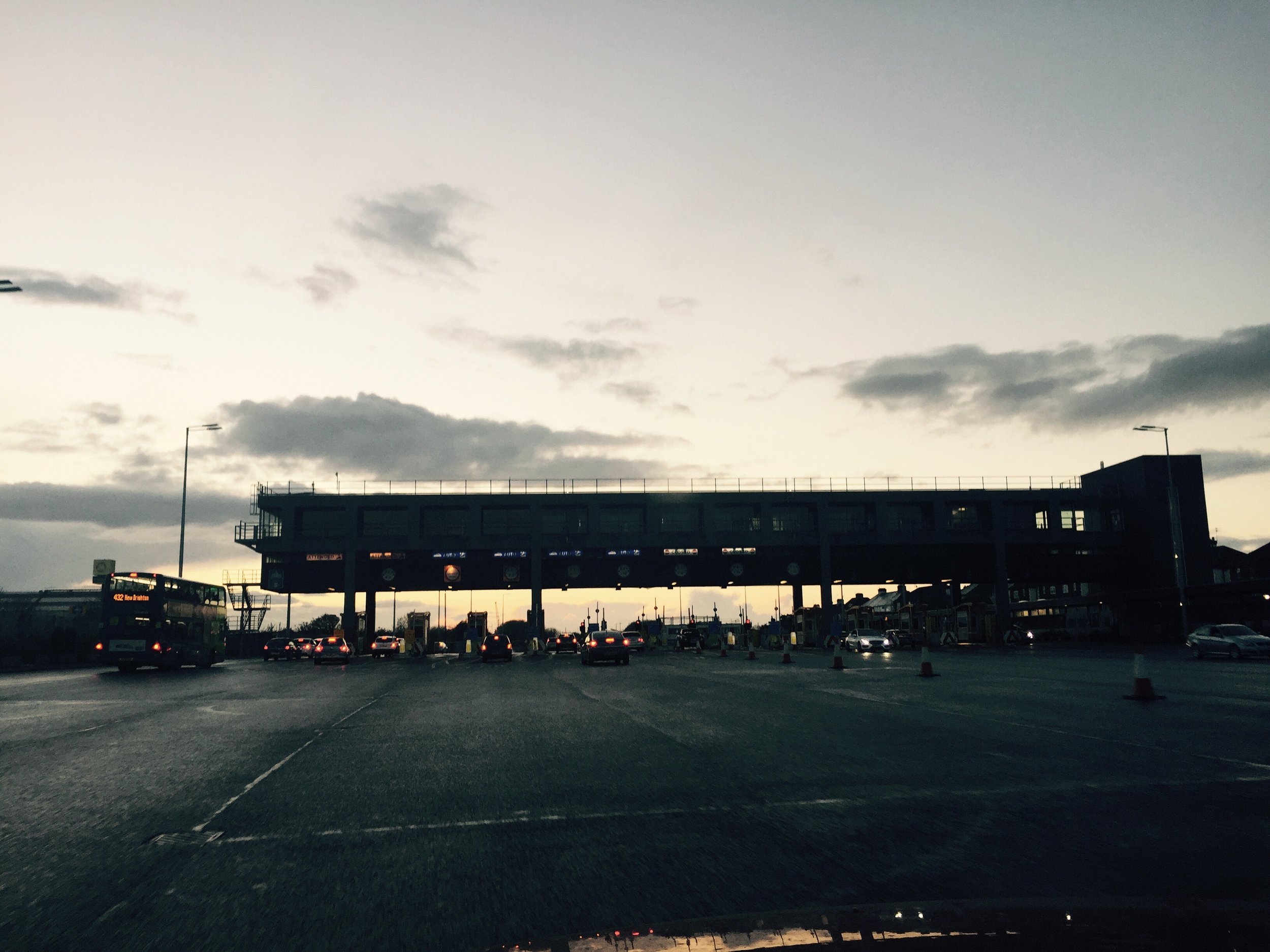
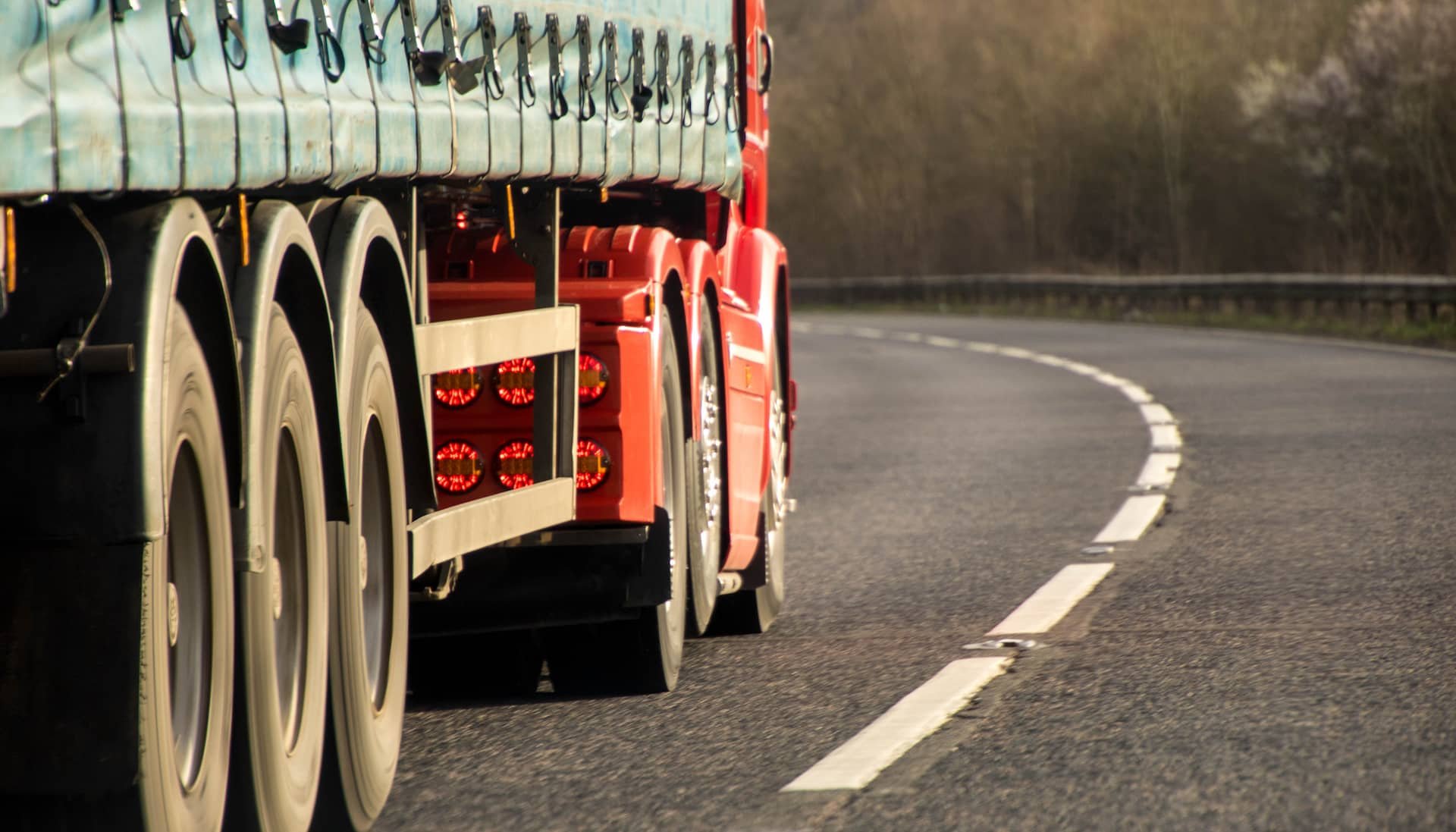